Blog
Filter By
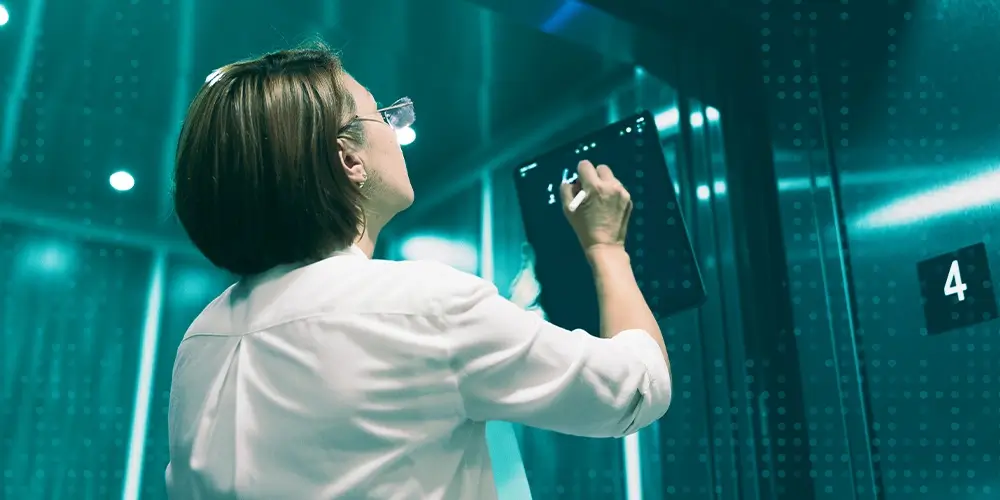
Elevators
4 min read
How to Efficiently Manage Elevator Safety Tests
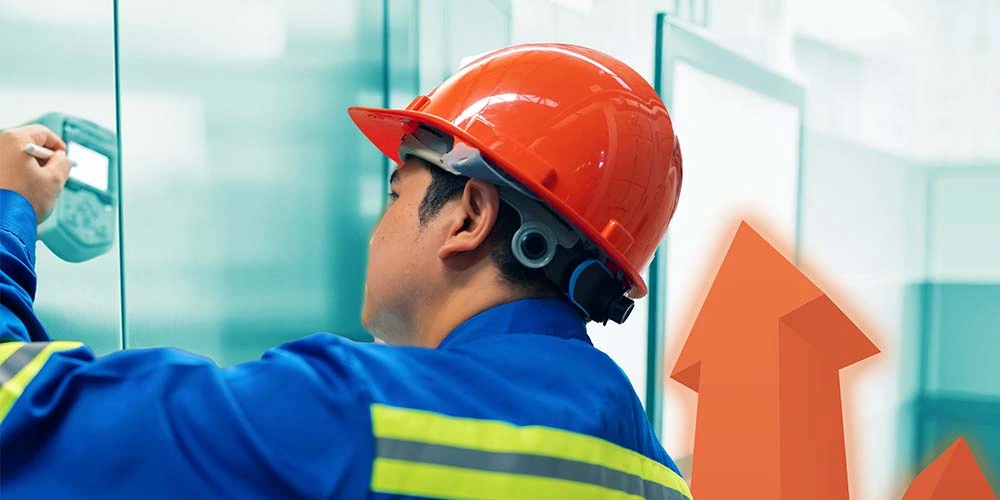
General
5 min read
How to Keep Elevator Mechanics in Sync with the Office
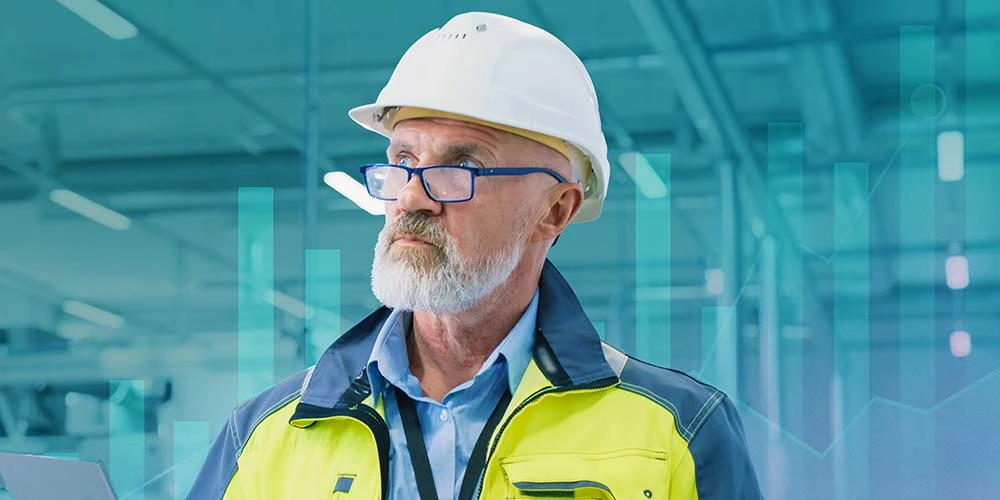
Cloud
6 min read
How to Overcome the Challenge of the Aging Workforce
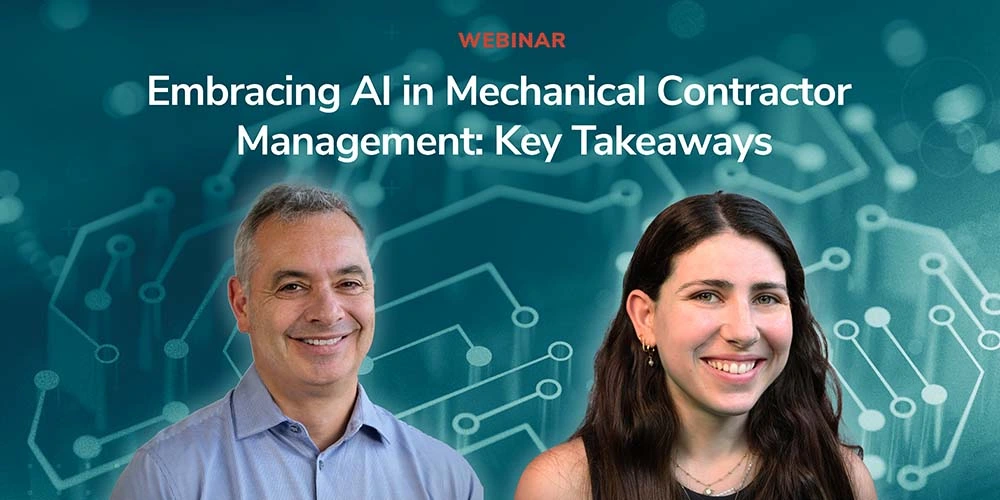
General
8 min read
Embracing AI in Mechanical Contractor Management: Key Webinar Takeaways
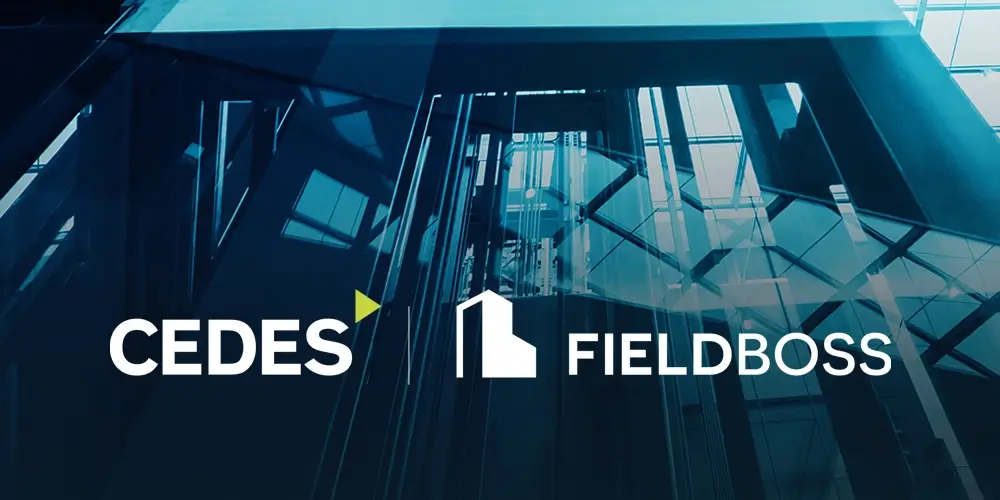
FIELDBOSS
4 min read
Connecting Insights to Actions for Smarter Elevator Service
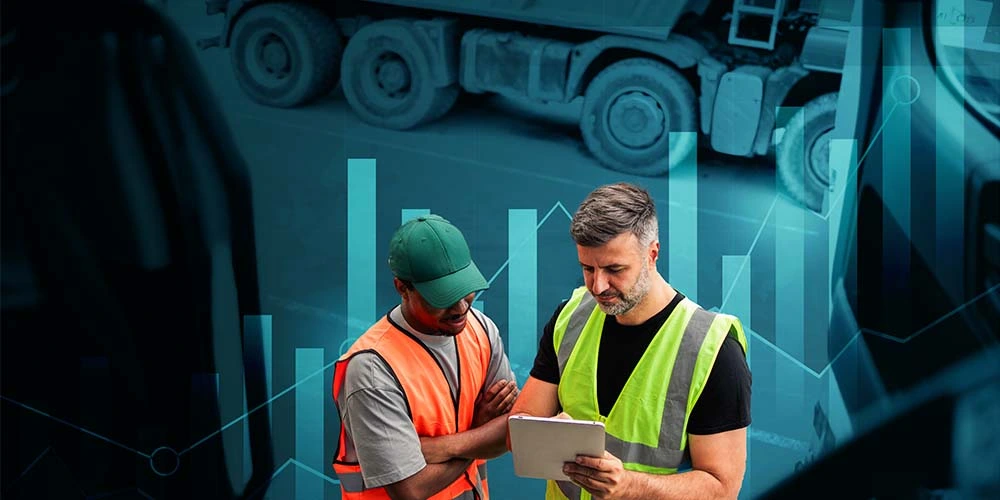
AI
8 min read
Top 5 Benefits of AI-Powered Route Optimization for Field Service Teams
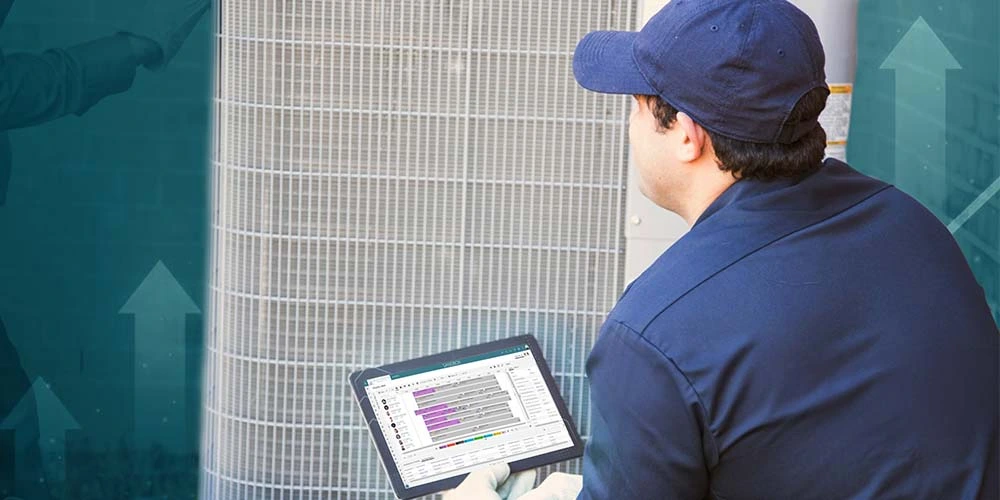
Elevators
11 min read
How to Simplify Elevator and HVAC Maintenance Contract Management with FIELDBOSS
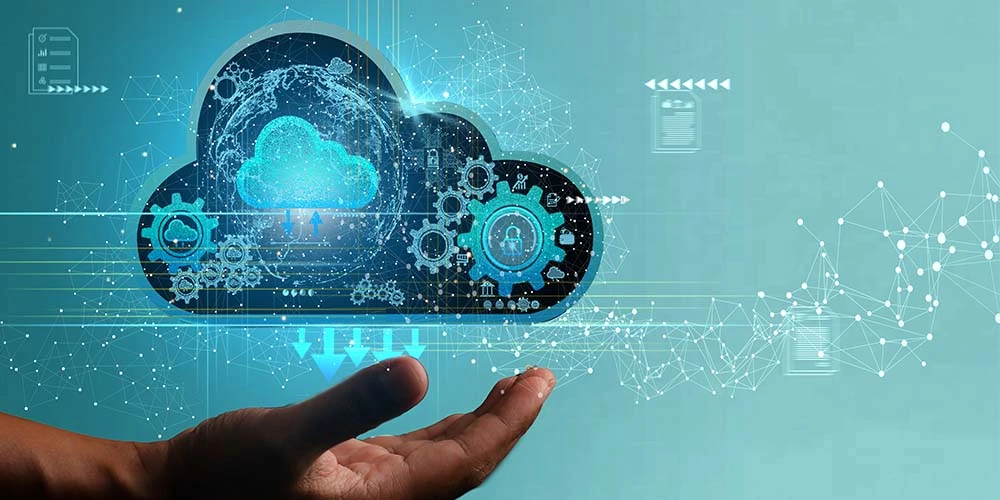
Cloud
8 min read
What Does Being “All In” on the Microsoft Cloud Platform Really Mean?
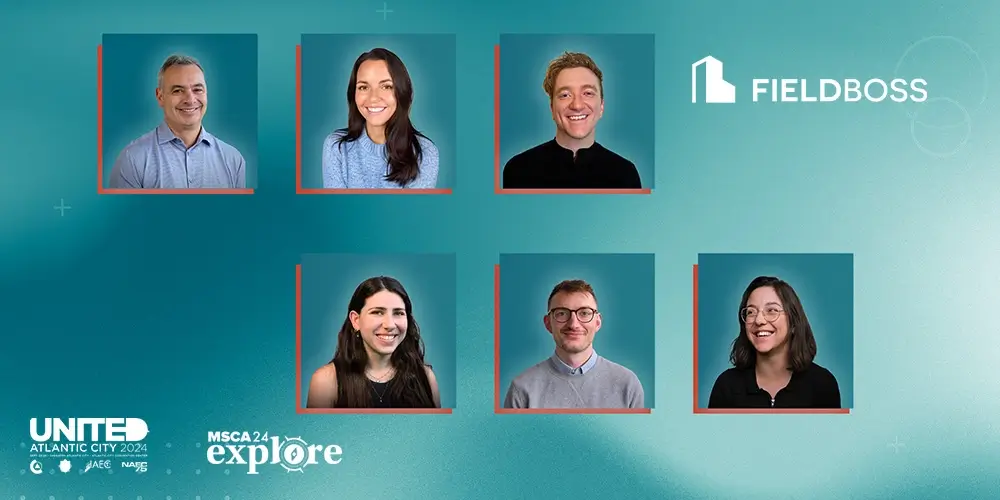
General
8 min read